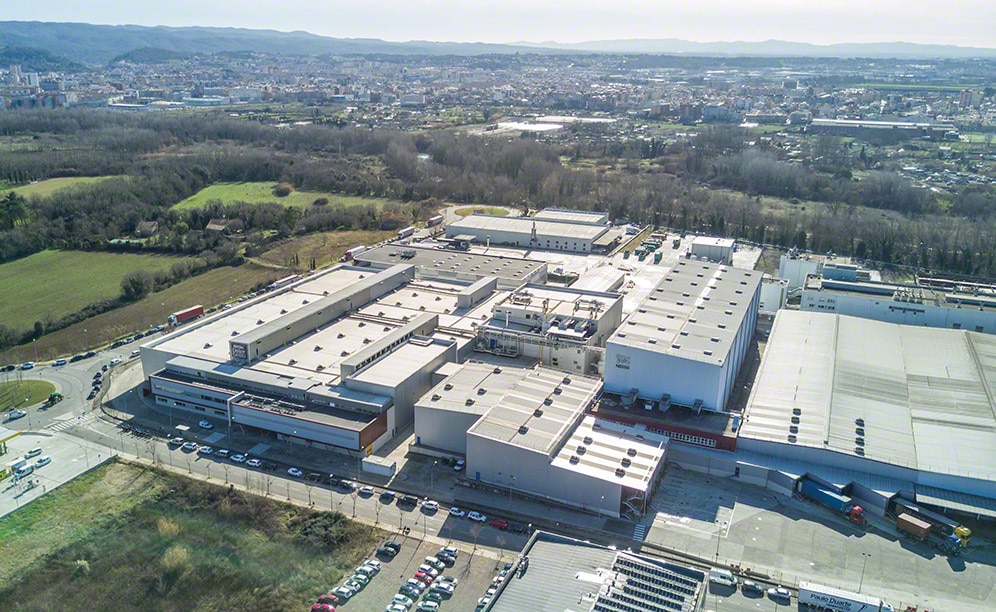
Nestlé acelera su fábrica de Dolce Gusto con sistemas de transporte automático
Un eficiente sistema de transporte de Mecalux en el centro de producción de Nestlé en Girona
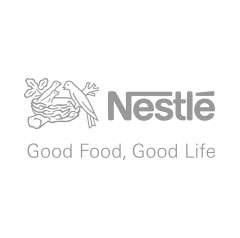
La fábrica de Nescafé en Girona (España) es uno de los centros de producción más competitivos que Nestlé posee en el mundo. Es un proyecto muy ambicioso, en constante expansión con el fin de adaptarse a las nuevas necesidades del mercado. Desde 1990, Mecalux ha colaborado con Nestlé en este centro, diseñando e implementando las soluciones más eficientes para mejorar su logística y fortalecer sus perspectivas de futuro.
Sobre Nestlé y Nescafé
Nestlé es la empresa de alimentación y bebidas líder en el mundo, con una presencia comercial que abarca más de 191 países. Cuenta con cerca de 2.000 marcas que ofrecen una gran variedad de productos: alimentos para bebés, agua embotellada, cereales para el desayuno, café y té, confitería, productos lácteos, alimentos para mascotas o aperitivos, entre otros.
Actualmente, posee diez centros de producción en España, distribuidos en cinco comunidades autónomas. Estas fábricas sobresalen por su alto rendimiento y exportan el 44% de su producción a otros países.
En 1968, Nestlé construyó un centro de producción en Girona (España) donde se fabrica el café soluble de Nescafé y, desde 2009, también las cápsulas de Nescafé Dolce Gusto. Este centro ha experimentado un gran crecimiento a lo largo de los últimos años, hasta convertirse en la mayor planta de producción de café soluble de la multinacional.
Nescafé es la marca de café instantáneo propiedad de Nestlé. Se lanzó en 1938 y, desde entonces, ha ampliado su catálogo introduciendo nuevas e innovadoras recetas y sabores para satisfacer cada gusto, ocasión o presupuesto.
Mecalux y Nestlé
La colaboración entre las dos compañías se inició en 1990, cuando Mecalux construyó un almacén automático autoportante para palets en la fábrica de Nescafé en Girona.
Este almacén, de 25 m de altura y 107 m de longitud, está compuesto por siete pasillos con estanterías de simple profundidad a ambos lados que ofrecen una capacidad de almacenaje para 16.380 palets. Allí se alojan los productos terminados, listos para ser enviados a expediciones.
Unos años más tarde, en 2006, Mecalux erigió un segundo almacén autoportante de 21 m de altura, a pocos metros de distancia del primer almacén. Está formado por dos pasillos con estanterías de simple profundidad donde se depositan un total de 740 contenedores con materias primas.
El almacén está adaptado a las medidas y características de los contenedores con los que trabaja Nestlé: miden 1.210 x 1.060 x 1.810 mm y no tienen patines. La entrada y salida es automática, mediante unos transportadores que conducen la mercancía directamente hasta el extremo de ambos pasillos de almacenaje. Para facilitar su traslado sobre los transportadores, los contenedores se colocan encima de un palet esclavo.
Asimismo, los estantes disponen de soportes que posibilitan que los contenedores se apoyen encima sin necesitar el palet esclavo.
Nescafé Dolce Gusto
Nestlé empezó a comercializar las cápsulas de té y café Nescafé Dolce Gusto en 2005. Inicialmente, el centro de producción se encontraba en Reino Unido, pero tras la buena aceptación del producto en España, la compañía decidió instalar una nueva fábrica en este país a fin de abastecer este mercado con mayor rapidez.
La empresa amplió el centro de producción de Girona en 2009 y construyó la fábrica de Nescafé Dolce Gusto al lado de las instalaciones ya existentes. Con la colaboración de Mecalux, este centro se ha ido ampliando y adaptando, en distintas etapas, a los nuevos requisitos presentados por Nestlé:
Primera intervención
La compañía solicitó el asesoramiento de Mecalux con el objetivo de comunicar la nueva fábrica de Nescafé Dolce Gusto con el almacén de productos terminados. Precisaba un sistema de transporte ágil que le proporcionara un flujo de movimientos constante entre ambos puntos. El proyecto suponía todo un reto, ya que debían conectarse dos naves separadas entre sí por una calle. Mecalux propuso la construcción de un puente elevado y cubierto –a 6 m de altura respecto al suelo– que uniera los dos edificios, con un circuito de transportadores ubicado en el interior.
Esta solución evita interferencias con la circulación habitual y, a su vez, los productos quedan protegidos de la intemperie. Los transportadores de rodillos se desplazan a una velocidad de 20 m/min. Su funcionamiento es completamente automático y requieren una mínima intervención de operarios, eliminando la posibilidad de errores derivados de la gestión manual.
Segunda intervención
En 2011, Nestlé instaló dos elevadores más que conectan las dos plantas del centro de producción.
Un circuito de transportadores dirige la mercancía directamente hasta los elevadores. Los transportadores se hallan a una altura más elevada, sustentados por una estructura resistente que garantiza su estabilidad.
De este modo, se ha logrado aprovechar la superficie del centro de producción, así como evitar interferencias con las demás operativas.
Tercera intervención
Ante el incremento de las ventas de Nescafé Dolce Gusto, en 2012, la compañía necesitaba aumentar el número de movimientos de palets entre el centro de producción y el almacén de producto terminado.
Para ello, Mecalux suministró un nuevo elevador en la salida de producción que duplica la cantidad inicial de palets movidos.
Cuarta intervención
Nestlé precisaba conectar el centro de producción con la nave de expediciones, para enviar la mercancía directamente hasta allí, sin entrar en el almacén.
Mecalux instaló una nueva salida en el circuito de transportadores que abandona el centro de producción. La mercancía cruza el puente elevado y, antes de llegar al almacén, un elevador desciende los palets correspondientes hasta expediciones.
La compañía requería automatizar el área de expediciones, para así maximizar el rendimiento de todas las operativas que allí tienen lugar:
- Zona de remontado. Una lanzadera distribuye los palets en seis transportadores, donde quedan a la espera de dirigirse a la máquina automática de remontado que apila un palet encima de otro.
- Canales de precargas. Otra lanzadera recoge los palets apilados y los distribuye en seis canales de precargas, formados por transportadores de rodillos con una ligera inclinación. Este sistema agrupa los palets de un mismo pedido o ruta.
- Precargas en el suelo. Justo enfrente de los canales dinámicos, se ha habilitado una zona de precargas en el suelo. Los palets se preparan antes de cargar el camión de transporte y distribución; de este modo, se evitan tiempos de espera en las salidas de la mercancía procedente del almacén.
Quinta intervención
Junto a la nave de expediciones, se ubica el almacén de big-bags o sacos industriales con materias primas. Estos sacos se colocan sobre palets para facilitar su traslado y almacenaje en las estanterías.
La entrada al almacén es automática, mediante un circuito de transportadores. Los palets cruzan un puesto de inspección en el que se verifica su estado y que su peso y medidas se correspondan con los requisitos de calidad establecidos.
A continuación, un elevador traslada la mercancía hasta la planta superior, donde se encuentran dos bloques de estanterías de paletización compacta drive-in.
Las estanterías se componen de un conjunto de calles de 6,5 m de altura, cada una de ellas con tres niveles. Por su parte, cada nivel cuenta con carriles de apoyo fabricados con chapa de acero galvanizado de elevada resistencia donde se depositan los palets con los sacos encima.
Software de control
Ante la envergadura de este centro de producción, es fundamental un sistema informatizado que controle y dirija todos los movimientos de los equipos de manutención automáticos que se han instalado.
Mecalux ha implementado el módulo de control Galileo, encargado de dar las órdenes a los transportadores, lanzaderas y elevadores para que se desplacen de forma continua y controlada.
Galileo posee una interfaz muy intuitiva y es capaz de simular el funcionamiento electromecánico de la instalación automática completa a través de un SCADA.
Está en comunicación continua y bidireccional con el software de gestión de almacenes y con el ERP de Nestlé. Como resultado, la empresa ha logrado maximizar la rentabilidad de todos los procesos que se llevan a cabo en su centro de producción.
Beneficios para Nestlé
- Eficiente sistema de transporte: los transportadores aportan mucha rapidez en el traslado de la mercancía hacia las distintas áreas del centro de producción y el almacén.
- Flujo de mercancía elevado: el circuito de transportadores automáticos y los elevadores proporcionan el número de movimientos de palets necesarios para Nestlé.
- Instalación segura: los elementos automáticos están protegidos para evitar incidentes, así como el acceso de personal no autorizado.
Galería
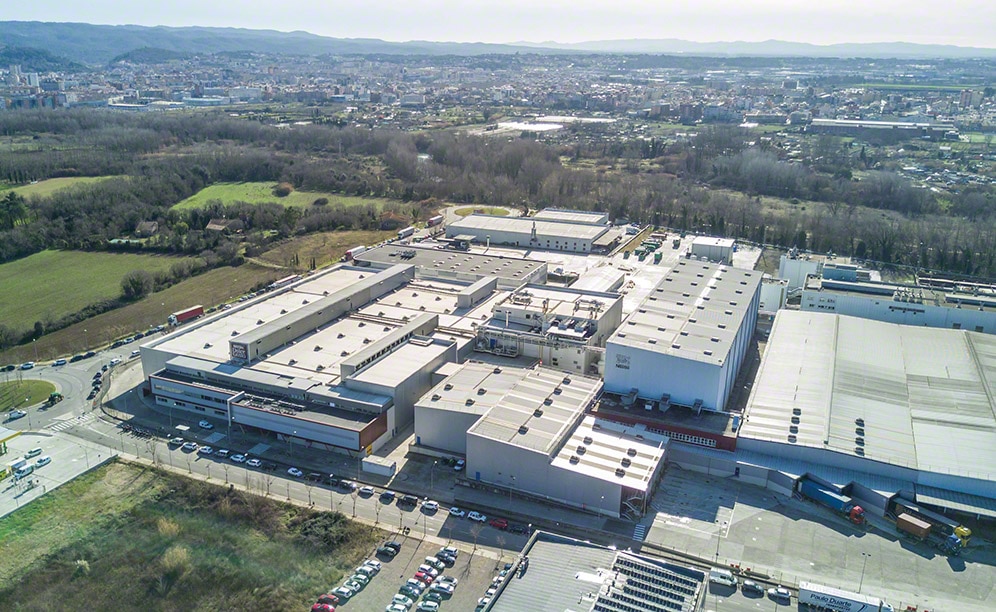
Mecalux construyó un almacén automático autoportante para palets en la fábrica de Nescafé en Girona
Consulte con un experto