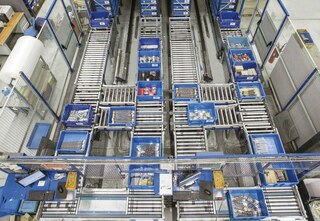
Método Kanban: ¿qué es y cómo funciona en logística?
El método Kanban se encarga de organizar el abastecimiento y la producción de bienes en procesos de fabricación que operan bajo la metodología just-in-time (JIT), que es cuando se dispone solo de la materia prima necesaria en el momento adecuado. El objetivo final es ajustar la capacidad de fabricación a la demanda para evitar el sobrestock y las esperas innecesarias entre procesos.
Es en la japonesa Toyota donde se idea el sistema Kanban en los años cincuenta, como parte de la metodología Lean manufacturing (minimizar el desperdicio para aumentar la productividad). El ingeniero industrial Taiichi Ohno fue quien diseñó este modelo de producción, que se reveló como la solución para hacer frente a la profunda depresión en la que se había hundido la industria japonesa tras la Segunda Guerra Mundial.
¿Qué es el sistema Kanban? Definición y origen
El método Kanban establece un protocolo para la reposición de stock. Es un sistema de comunicación de órdenes de producción y de reposición de materiales. Se utiliza en modelos de producción que responden de manera directa a la demanda (sistema pull, el producto no se empieza a fabricar hasta que la planta de producción recibe el pedido en firme del cliente).
Taiichi Ohno concibió el sistema Kanban inspirándose en las reglas de reposición de los supermercados americanos. En ellos, los clientes retiran los productos de las estanterías. Cada producto está etiquetado y, al pasar por caja, esta recopila todas las referencias vendidas y emite una orden de reposición al almacén, que identifica la mercadería con el mismo sistema. Una vez repuestos los artículos en el supermercado, el almacén envía, a su vez, otra orden de reposición a sus proveedores o fabricantes, y así sucesivamente a lo largo de toda la cadena de suministro. Para determinar en qué momento se disparan las órdenes de reposición se emplea el sistema de punto de pedido.
¿Cómo funciona? Las tarjetas y los tableros Kanban
La traducción literal de Kanban en japonés es “tarjetas de colores”. Esto es así porque, originalmente, se usaban cartulinas para solicitar al proceso anterior las piezas que se necesitaban. Cuando se completaba la orden de reposición, la tarjeta Kanban volvía al casillero original.
Estas tarjetas recogían la información que identificaba cada lote de material: SKU, código, tamaño de lote, destino de la mercadería, cliente que lo ha solicitado… Las tarjetas se colgaban en cada uno de los contenedores o estantes donde se hallaba el producto.
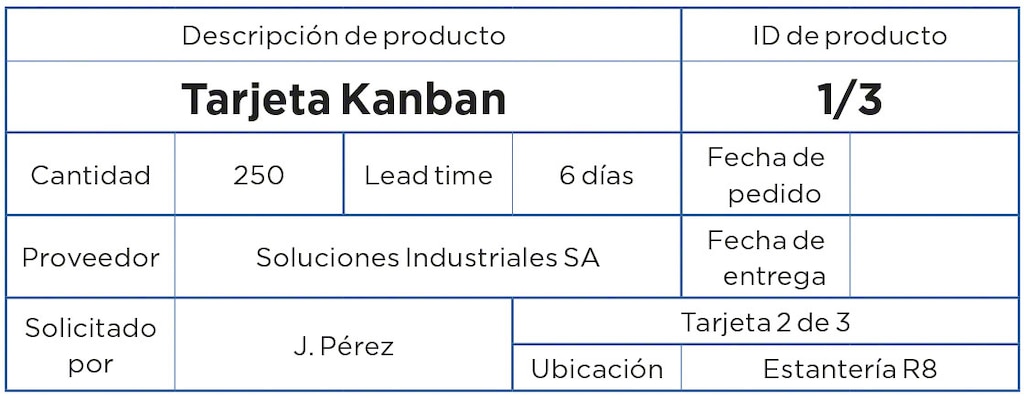
Hoy en día, el sistema Kanban ha sido sustituido por aplicaciones informáticas, que son las que desencadenan el proceso de reabastecimiento. El sistema de trabajo también se puede representar mediante tableros Kanban, que constan de varias columnas donde situar las tarjetas o etiquetas virtuales. De esta forma, cada columna indica el estado en que se encuentra cada tarea y a quién le corresponde ejecutarla.
Aunque el método Kanban surgió originalmente en un contexto industrial, actualmente también se aplica en la gestión de todo tipo de proyectos como, por ejemplo, aquellos relacionados con el desarrollo de software.
Tipos de tarjetas de Kanban
Existen dos principales tipos de tarjetas Kanban:
- Kanban de transporte: marca cuánto producto hay que reponer para cumplir con el siguiente proceso en la cadena. Si tomamos el ejemplo del supermercado, la tarjeta Kanban de transporte se utilizaría para indicar que un tipo de producto se ha vendido y tiene que ser trasladado del almacén al lineal de la tienda.
- Kanban de producción: se usa para solicitar la fabricación de un producto. Con el mismo ejemplo, este tipo de tarjeta Kanban la emitiría el almacén al quedarse sin stock (porque ya lo ha mandado a tienda).
En el siguiente diagrama, vemos de forma esquemática el funcionamiento encadenado de las tarjetas Kanban de producción y transporte en una línea de fabricación simplificada:
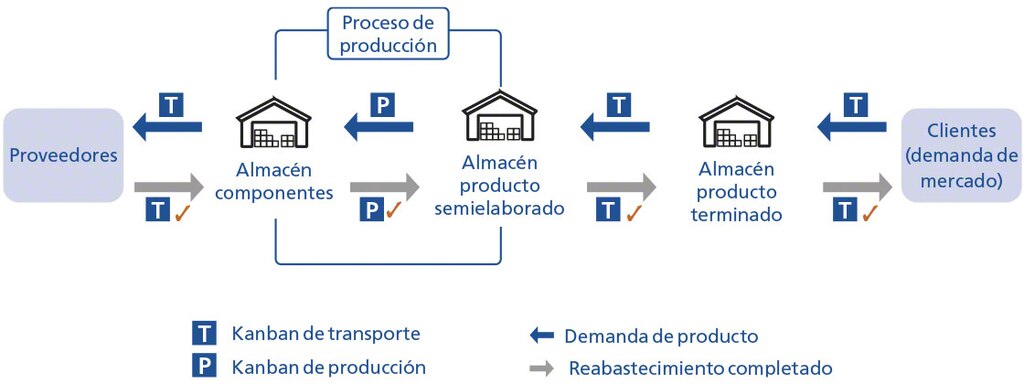
Ventajas de usar el sistema Kanban en logística y producción
El método Kanban es el aliado perfecto del sistema just-in-time o justo a tiempo porque:
- Permite visualizar el desarrollo del trabajo y así identificar cada fase del ciclo de producción o reaprovisionamiento con facilidad.
- Con el sistema Kanban es sencillo fijar el límite del trabajo en curso (también llamado WIP, work in progress) para prevenir que se formen cuellos de botella.
- Se puede medir el lead time entre procesos, es decir, el tiempo que se tarda en completar cada fase.
- Al enlazar las distintas etapas, funciona como un sistema de control de la producción y de los materiales disponibles en las diferentes instalaciones de almacenaje.
- Se evita caer en situaciones de sobreproducción o exceso de stock, lo que genera un ahorro de espacio de almacenaje.
Desventajas de emplear Kanban
Algunas de sus restricciones hacen que no siempre resulte el método más adecuado:
- El sistema Kanban proporciona resultados óptimos cuando el flujo de producción se distribuye de manera homogénea a lo largo del año y se organiza en series cortas con volúmenes similares. En cambio, si el negocio está sometido a una elevada volatilidad de la demanda que exige ajustes bruscos en la producción, el método Kanban experimenta ineficiencias que desaconsejan su utilización.
- Puede agravar retrasos en la cadena de producción si alguno de los eslabones falla (se pierde una tarjeta o se emite mal una orden, por ejemplo).
- El sistema Kanban no es el más flexible para hacer frente a cambios importantes en las técnicas de fabricación de los productos.
- No funciona correctamente si los proveedores no aplican las mismas reglas Kanban para el reaprovisionamiento.
¿Cuándo usar Kanban en el almacén? El papel del WMS
En la actualidad, la aplicación del método Kanban en el almacén ha dejado atrás las tarjetas de papel: ahora se aplica en las organizaciones mediante un sistema de gestión del almacén (como Easy WMS) en combinación con sistemas de identificación automática como los códigos de barras o RFID. Cada registro en el WMS funciona como una tarjeta Kanban, ya que, al leer los datos con un escáner, el sistema devuelve toda la información ligada a ese SKU.
En logística, el método Kanban se utiliza para organizar el reaprovisionamiento de stock a distintos niveles:
Kanban en un mismo almacén
Si las ubicaciones dedicadas al picking y las de almacenamiento están divididas, el sistema Kanban es especialmente útil para la reposición de stock de las estanterías de picking.
Una vez que se agoten las referencias en esas ubicaciones de picking, el WMS emite un aviso automático para la reposición que funciona como una tarjeta Kanban, aunque también puede activarlo de forma manual cualquier operario al detectar la falta de material.
De este modo, el cambio de ubicación de la mercadería se programará en función de la prioridad, aunque suele reservarse para los momentos valle de la instalación (por ejemplo, así ocurre en el picking por olas o wave picking).
Si al hacer el traslado de mercadería de almacenamiento a picking se observa que las referencias se han terminado también en la zona de almacenaje, el WMS puede enviar una notificación directa al departamento de compras para que lo tengan en cuenta en las solicitudes de pedidos a proveedores.
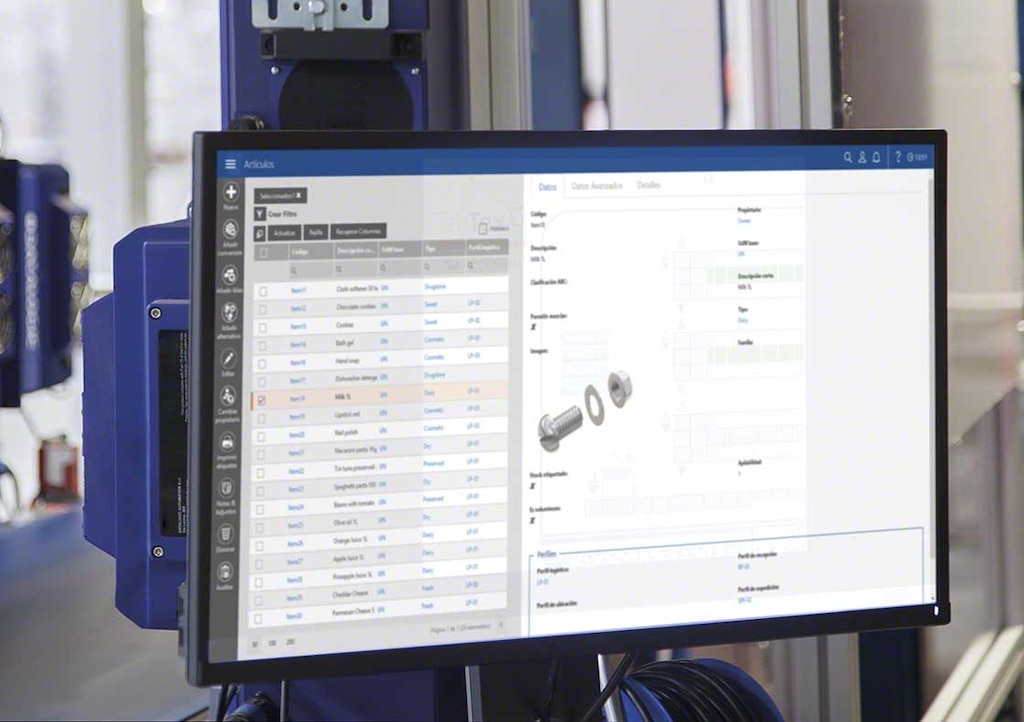
Kanban en una red de almacenes logísticos
El método Kanban también se puede aplicar en empresas que trabajan con un inventario distribuido en varios centros de almacenaje. Estos pueden servir a una misma línea de producción (como en logística de producción) o formar parte de la misma red logística (como en redes logísticas retail).
Veamos en detalle cómo funciona el Kanban en cada caso y qué funciones desempeña el WMS:
- Kanban en almacenes de producción: la principal particularidad de las instalaciones que surten a fábricas es que manejan stocks clasificados como materias primas, semielaborados y productos acabados. Para controlar que no se produzca ninguna rotura de stock en el proceso productivo, es fundamental mantener un control de stock informatizado. En este sentido, el SGA para producción opera siguiendo el método Kanban ya que, ante un nuevo pedido, el WMS lanza órdenes de trabajo a fábrica y monitoriza el stock de seguridad disponible de cada referencia.
- Kanban en cadenas de suministro del retail: en este caso, la red logística está compuesta por almacenes (centrales y regionales) y tiendas físicas. Siguiendo el método Kanban, la demanda de los productos se registra en el punto de venta y, desde él, se generan las órdenes de reposición a los almacenes. Aquí el WMS funciona como un catalizador del reaprovisionamiento entre centros, puesto que contiene los datos globales de stock. Además, si tomamos el ejemplo de Easy WMS de Mecalux, con el módulo Store Fulfillment es posible organizar y ordenar movimientos de stocks entre centros sin intermediarios: esto permite aprovechar al máximo la capacidad logística de la empresa.
Gestión de stock con el método Kanban
Aplicar el sistema Kanban tradicional con extensos inventarios distribuidos entre distintos centros y manejando un volumen muy alto de SKU resulta ineficiente debido a la creciente complejidad. No obstante, es posible poder planificar la reposición de stock y aprovechar las ventajas del método Kanban con la ayuda de un WMS.
Easy WMS cuenta con avanzadas funcionalidades para la gestión de stock integrada y permite operar con distintas reglas de reposiciones. Si quieres profundizar en el funcionamiento de nuestro WMS, ponte en contacto con nosotros y uno de nuestros especialistas te enseñará detenidamente cómo puede contribuir a la gestión optimizada de tu almacén.